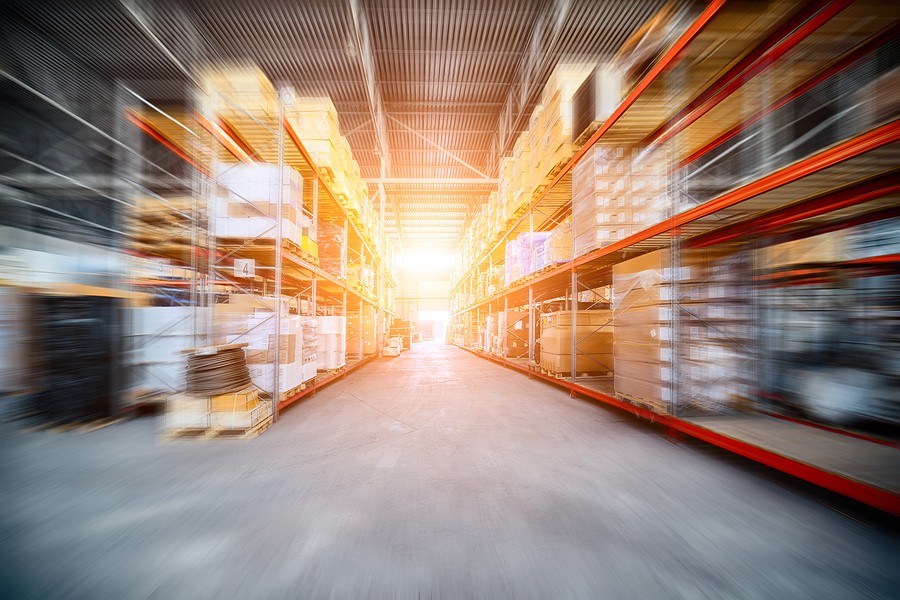
Rack safety is an important matter for any warehouse. A design flaw, unnoticed damage, improper assembly, or overloading can very quickly lead to a collapse. Therefore, proper techniques are essential to keeping employees safe while working near racks, as well as protecting your goods. Here, Barclay Brand Ferdon, which serves North and Central New Jersey and parts of New York, provides some lifesaving rack safety tips to implement at your facility.
Design and Construction
Rack safety begins at the design phase. Even a small fault in the engineering can weaken the entire frame, leading to accidents further down the road. This is why you should always use a qualified rack engineer when designing and assembling your system. Here are a few other ways to ensure a safe design that will last:
- Don’t opt for the least expensive option on the market.
- Fully inspect a structure before purchasing it for your facility.
- Consider accessories and enhancements like doubled columns, larger base plates, or column protectors, which will improve your rack’s longevity.
Further, you should never reconfigure your racks without authorization from the original manufacturer and consulting with a qualified engineer. If you build onto the structure, use components from the same manufacturer to ensure compatibility. Finally, make sure your original load application and rack configuration drawings are kept updated with all modifications – even minor ones.
Proper Training and Use
Once your racking systems are in place, it’s essential to train employees on how to use them properly. Include personnel working around and within the racks, as well as lift truck operators who will be placing or removing loads from the system. A few safety practices to follow include:
- Don’t overload the racks.
- Use equipment that was designed to interface with your system.
- Bolster your racking with the right accessories.
- Prioritize safety over speed to avoid user errors.
- Keep the facility and aisles uncluttered.
- Make sure the aisles are wide enough to traverse without collisions.
- Immediately report any visible damage or deterioration.
To make sure your employees follow good safety practices, incentivize them with rewards. Also, regularly label your racks with guidelines on proper use to give employees a reminder of the protocols to follow while in and around the racks, reducing the risk of error-related accidents.
Regular Inspections
Finally, ensure that your supervisors conduct regular inspections of your racks and review rack logs, including previous inspection notes and comments from employees about potential hazards. Then, they should tour the racks themselves and watch for anything dangerous. Risk factors to look for include:
- Signs of damage or deterioration on the racking system
- Improperly placed, double-stacked, or damaged pallets
- Warning signs of failure, like excessive beam deflections
- Overloading at any position or in the system as a whole
- Improper loading techniques used by employees
- Modifications not approved by an engineer or recorded
Inspections should focus on the most at-risk sections, such as high-traffic areas, narrow aisles, transfer aisles, cold environments, and locations that have sustained prior damage. The results should then be recorded and kept on file. If any unsafe conditions are found, the entire rack must be unloaded, assessed by an engineer, and immediately repaired or replaced.
Prioritize Workplace Safety with Barclay Brand Ferdon
At Barclay Brand Ferdon, we believe that ensuring racking systems safety should be the top priority for all of our clients. To help, we supply high-quality warehouse solutions that are customizable to specific needs and approved by our team of experienced engineers. To learn more about rack safety, contact us today.