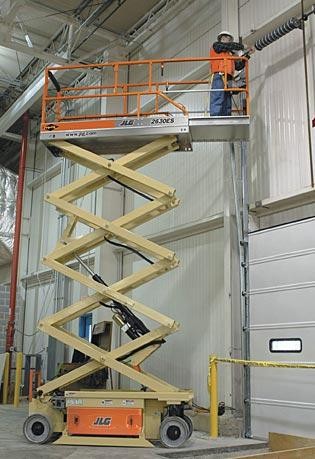
According to the national Census of Fatal Occupational Injuries, 887 workers died from falls in 2017 – the highest number of deaths since they started tracking in 1992. In 2016, the Occupational Safety and Health Administration (OSHA) set forth new fall protection standards in an attempt to combat the rising trend of workplace deaths from falls. If you’re like a lot of businesses, you may still be working toward full compliance with these new rules, but it is crucial that you do for the safety of your workers. And it’s especially true if your employees need to reach high places with aerial equipment from Barclay Brand Ferdon, such as an order or stock picker, man up turret truck, scissor lift, boom lift, or aerial work platform because they’re at much greater risk of death from a fall. Here’s a guide to the safety standards you should have in place for workers using aerial equipment.
Which Standards Apply to Aerial Equipment?
With all of the other things you have on your mind while running your business, OSHA standards can be intimidating, but they can’t be ignored. It helps to know exactly which standards apply to your situation so that you can drill down into the information, knowing you’re in the right section.
For aerial equipment, the standards that specifically apply are: 29 CFR 1910.67, 29 CFR 1910.269(p), 29 CFR 1926.21, 29 CFR 1926.453, 29 CFR 1926.502.
The new fall protection standards are for Walking-Working Surfaces and Personal Fall Protection Systems (29 CFR 1910 Subparts D&I), which also apply to those working with aerial equipment.
Understanding the Hazards and Providing Proper Training
One of the main changes with the new OSHA fall protection standards is that documented fall hazard risk assessments are now required. Your documentation will need to include the use of aerial equipment. And any employee who is exposed to fall hazards will need to have personal protective equipment such as lanyards & harnesses and be properly trained.
The hazards associated with operating aerial equipment aren’t limited to falls, of course. There are many others, including electrocution, structural failure, ejection from the platform, entanglement, and more. That’s why it is essential that only employees who are trained properly be allowed to operate the aerial equipment. OSHA also requires you to retrain any employee who is seen improperly operating an aerial lift or order picking lift truck.
Personal Fall Arrest and Fall Restraint Systems for Safe Operation of Aerial Equipment
From pre-start inspection to safe operation practices, there is a long list of things you need to do to ensure your employees remain safe. To prevent falls, employers must ensure that workers tie off at all times when working from an aerial lift. They can use a body belt or tether that’s anchored to the basket or boom or a body harness with a tether or lanyard in order to comply with OSHA regulations.
Get the High-Quality Aerial Equipment You Need from Barclay Brand Ferdon
If you’re looking for reliable ways to help your employees work safely in high places, Barclay Brand Ferdon offers a complete line up of OSHA Safety Training classes as well as the best aerial equipment, man-up lifts and stock pickers from three of the top manufacturers in the industry: Yale, JLG and Genie. We also supply a full line of accessories such as lanyards and harnesses to outfit your employees for safety in the warehouse. Call us at 908-223-8580 to learn more about our products and safety training programs or contact us online today.